Automate Stock Management,
Reduce Human Errors & Inaccuracies, Increase Profitability
Key Features And Functions Of Aplus Stock Control:
• Track Stock Level
• Barcode / QR Code Scanning
• Stock Management Reports
• Stock Classifications
• Stock Valuations Methods
• Consignment Stock
• Serial Number Tracking
• Item Batch Tracking
• Multi Location Management
• Integration with Point of Sale
• Integration with Accounting System
• Integration with Billing System
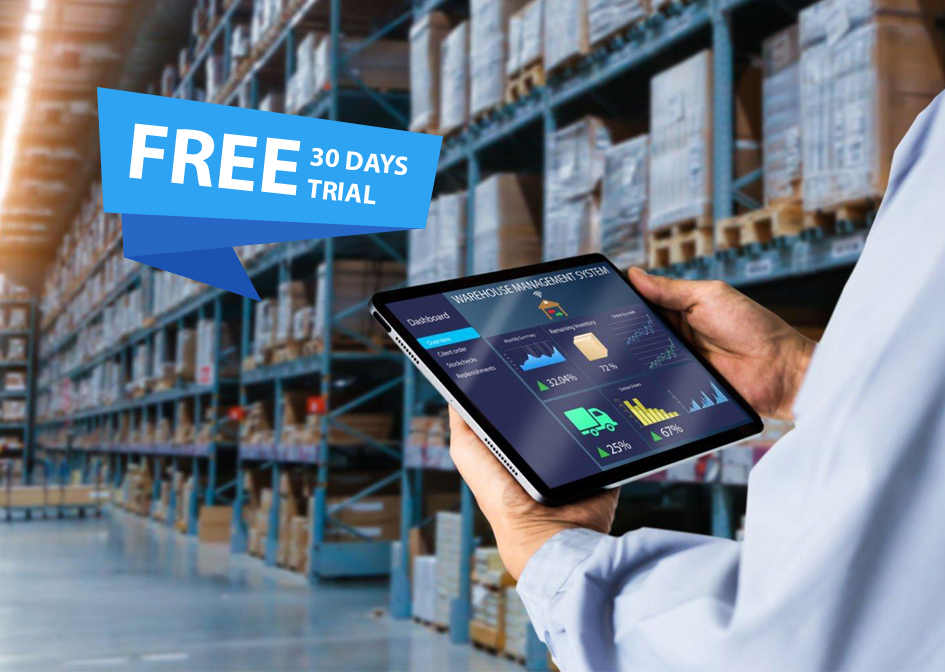
Automate inventory management, reduce handling costs, optimize cash flow
- Optimize Inventory Levels. Demand-based planning using historical demand, sales forecasts and seasonality ensures you have the right amount of stock.
- Boost Profitability. Managing inventory is more efficient and cost-effective with company-wide inventory visibility.
- Decrease Cost of Goods Sold. Intelligent fulfillment minimizes handling expenses and reduces shipping costs.
- Reduce Human Errors & Inaccuracies.
An effective inventory management system is crucial for businesses to efficiently track, control, and optimize their inventory levels. Below are some important functions and features that a comprehensive inventory management system should have:
Inventory Tracking: The system should offer real-time tracking of inventory levels, allowing users to monitor stock quantities accurately.
Barcode/QR Code Scanning: This feature enables quick and accurate data entry by scanning barcodes or QR codes on products, reducing the likelihood of manual errors.
Stock Alerts and Notifications: The system should be capable of sending alerts and notifications when inventory levels reach predefined thresholds, helping to avoid stockouts or overstocking.
Inventory Reports and Analytics: Comprehensive reporting and analytics functionalities provide insights into inventory turnover, slow-moving items, and other crucial data for making informed decisions.
Inventory Classification: The ability to categorize inventory items into different groups or categories simplifies organization and management.
Reorder Point and Reorder Quantity: The system should calculate and suggest optimal reorder points and quantities based on historical data and demand forecasts.
Batch and Lot Tracking: Especially important for industries with perishable or regulated goods, this feature allows tracking products by batch or lot numbers to facilitate recalls or expiry management.
Inventory Valuation Methods: Support for different inventory valuation methods like FIFO (First-In-First-Out) and LIFO (Last-In-First-Out) helps businesses manage costs and comply with accounting practices.
Integration with Point of Sale (POS): Integration with a POS system enables seamless updates of inventory levels when sales occur, minimizing the chances of overselling.
Multi-location Management: For businesses with multiple warehouses or stores, the system should handle inventory across all locations and allow easy transfer of goods between them.
Supplier Management: Keeping track of suppliers’ information and performance helps maintain good relationships and ensures timely replenishment.
Demand Forecasting: Utilizing historical data and trends to predict future demand helps optimize inventory levels and reduce carrying costs.
Serial Number Tracking: Useful for products with unique serial numbers, this feature allows tracing individual items through the supply chain.
User Access Control: Implementing role-based access control ensures that only authorized personnel can perform specific actions within the inventory system.
Mobile Access: Having a mobile app or responsive web design allows users to access and manage inventory on the go.
Automatic Data Synchronization: When integrated with other systems like sales, purchasing, or accounting, automatic data synchronization ensures consistent and up-to-date information across the organization.
Audit Trail: Maintaining a detailed log of inventory transactions helps in auditing and resolving any discrepancies.
Cloud-based Storage: Storing data on the cloud ensures data security, accessibility, and scalability.
Support and Training: Adequate customer support and training resources are vital for users to make the most of the inventory management system’s capabilities.
Scalability: The system should be able to accommodate the growing needs of the business without significant performance issues.
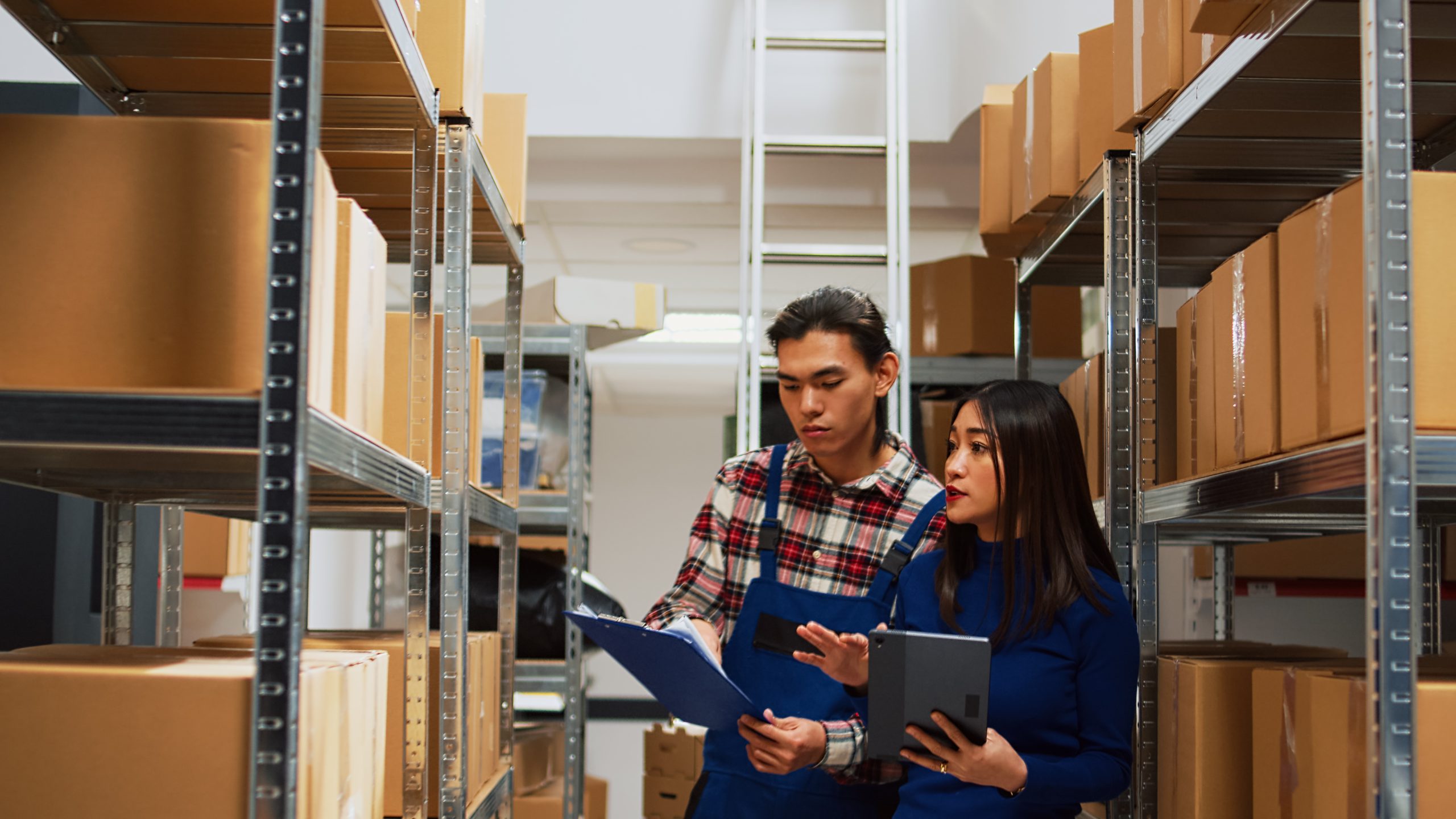
Each business’s specific requirements may vary, but a robust inventory management system with these functions and features can significantly improve efficiency, reduce costs, and enhance decision-making processes.
View your quantities on hand
Track stock value in real-time
Keep updated about your orders
Low stock alerts